
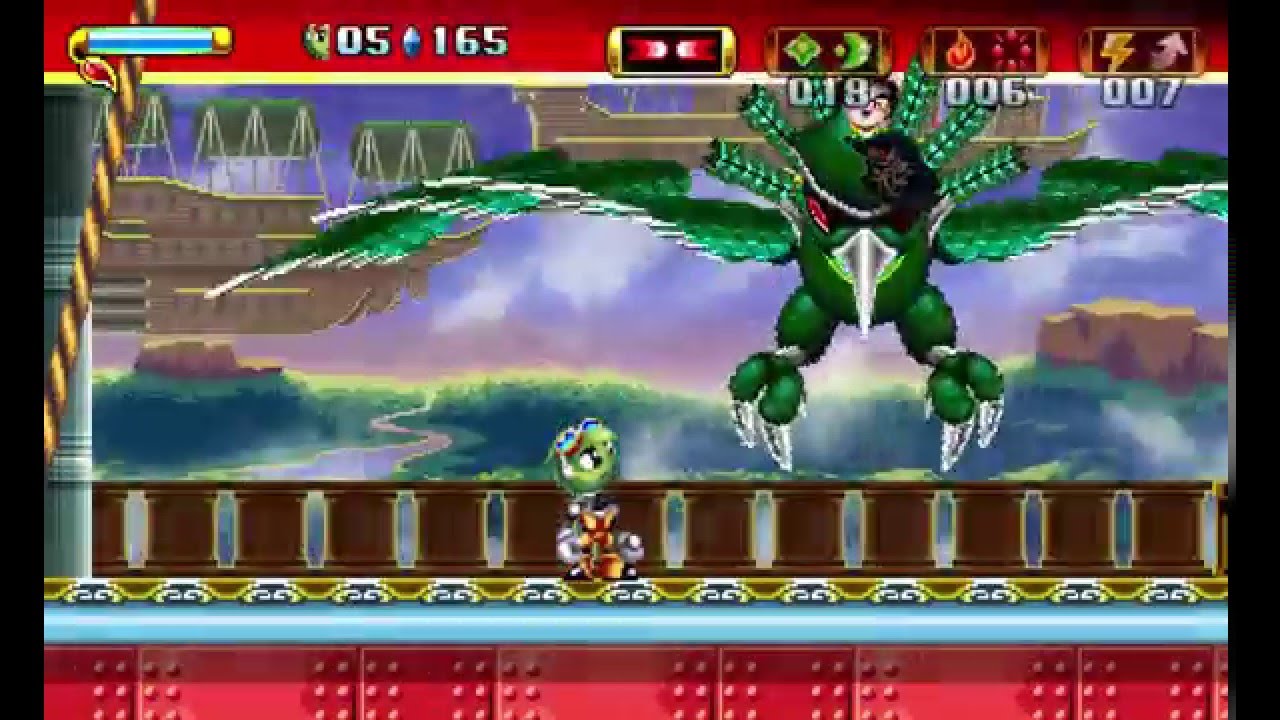
Progressive uprating of engine input power from 3600 to 4500 hp twin engine rating is allowed for in the design. One necessary change to the test stand involved gear trains of different ratio in the tail drive gearbox. The transmission fits within the NASA LeRC 3000 hp Test Stand and accepts the existing positions for engine inputs, main shaft, connecting drive shafts, and the cradle attachment points. It is demonstrated that in comparison with conventional helicopter transmission arrangements the split torque design offers: weight reduction of 15% reduction in drive train losses of 9% and improved reliability resulting from redundant drive paths between the two engines and the main shaft. The 3600 hp split- torque helicopter transmissionįinal design details of a helicopter transmission that is powered by GE twin T 700 engines each rated at 1800 hp are presented. The POC split torque tests demonstrated that face gears can be applied effectively in split torque rotorcraft transmissions, yielding good potential for significant weight, cost and reliability improvements over existing equipment using spiral bevel gearing. During the same tests, a 57% to 43% average distribution of the torque being recombined to the upper face gear from the lower face gear was measured between the two idlers. The final two pinion-two idler tests indicated 52% to 48% average torque split capabilities for the two pinions.
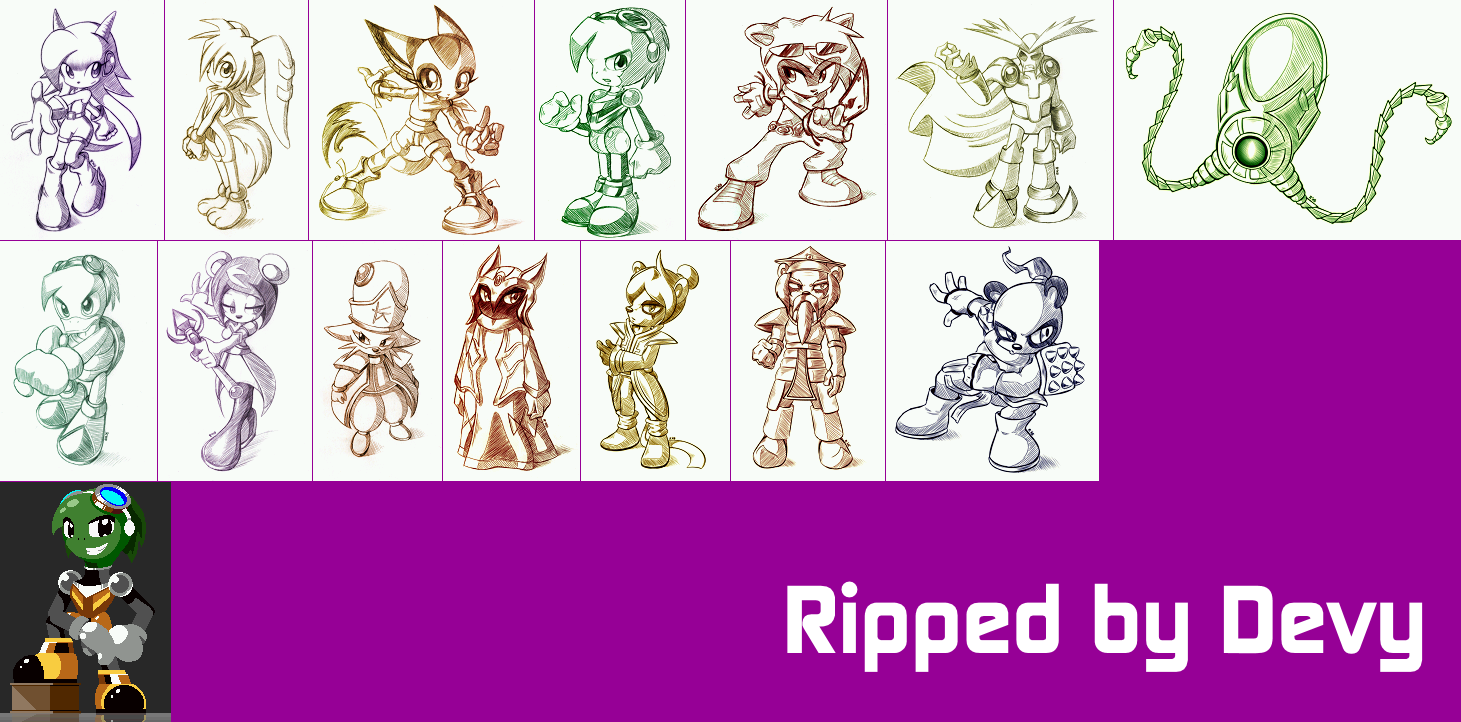
Strain gages applied in the tooth root fillets provided strain indication used to determine torque splitting conditions at the input pinions. A system of weights, pulleys and cables were used in the test rig to provide both the input and output loading. Resistance was applied at the output face gear to create the required loading conditions in the gear teeth. Two idler gears were also used in the configuration to recombine torque near the output. During tests, two input pinions were slow rolled while in mesh with the two face gears. The split torque tests were run using 200 N-m (1767 in-lbs) torque input to each side of the transmission. Design, manufacture and testing of the scaled-power TRP proof-of-concept (POC) split torque gearbox followed preliminary evaluations of the concept performed early in the program. This paper provides a summary of these cooperative tests, which were jointly funded by Boeing and DARPA. Tests of a 167 Kilowatt (224 Horsepower) split torque face gearbox were performed by the Boeing Company in Mesa, Arizona, while working under a Defense Advanced Research Projects Agency (DARPA) Technology Reinvestment Program (TRP). Torque Splitting by a Concentric Face Gear Transmissionįiller, Robert R. Also, dynamic analysis of this design predicts good load sharing and significant torsional response to accumulative pitch errors of the gears. A static analysis suggests increasing the helix angle of the input pinion of the thrust balancing design.
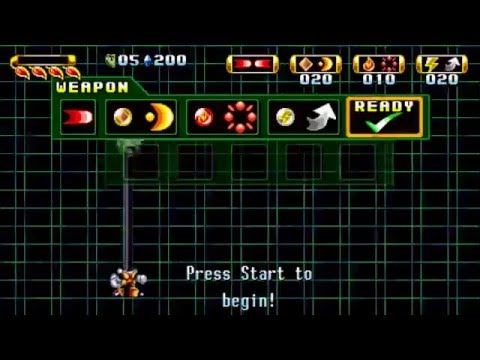
Friction forces that oppose the motion of the balance mechanism are significant. A thrust balancing load sharing device was evaluated.
FREEDOM PLANET TORQUE UNLOCK FULL
However, the elastomeric torque splitter as now configured is not capable over the full range of operating conditions of a fielded system. An elastomeric torque splitter that has large torsional compliance and damping produces even better load sharing while reducing dynamic transmission error and noise. Precise indexing and alignment of the geartrain to produce acceptable load sharing has been demonstrated. Two split torque designs that use different load sharing methods have been studied. The split torque designs can offer lighter weight and fewer parts but have not been used extensively for lack of experience, especially with obtaining proper load sharing.

Split torque transmissions are attractive alternatives to conventional planetary designs for helicopter transmissions.
